Automatic lubrication on all types of machines
Increase the life of your equipment
- Less grease used
- Preserves the environment
- Provides lubricant savings of up to 40%.
- Increases the availability of the equipment. Eliminates laborious operations (manual lubrication)
- No more forgotten lubrication points
- Increases accuracy
- Reduces repair and maintenance costs
- Eliminates equipment downtime costs and staff intervention
Lincoln automatic central lubrication
Lubrication systems
-
Lightweight and robust pump, forced pumping without depressurisation
-
Easy access and maintenance (jar, pumping element, electronic board, pressure relief valve)
-
Reliable and robust distributor: reinforced corrosion protection for distributor block and fittings
Progressive dispensing system
- Piston volumetric dispensing: dispenses measured amounts of lubricant at frequent intervals when machines are in operation, the lubrication schedule is then adhered to
- If grease is not dispensed to all points without exception, the system faults
- Emergency greasing
- Compatibility with other centralized greasing systems
- Simple, low-cost method of automating lubrication of bearings, shafts, and machine bearings
- Modular: > Reservoir volume (1Kg to 8 Kg) > 12 or 24V motor > Fixed or adjustable distributor (from 6 to 22 outlets) > On-pump or remote control box
- Options : > Fault detection : pressure switch on pump outlet or cycle sensor on distributor > Low level
Pump control: 12 or 24V control button or in-cab control box with dose display, level sensor, cycle forcing...
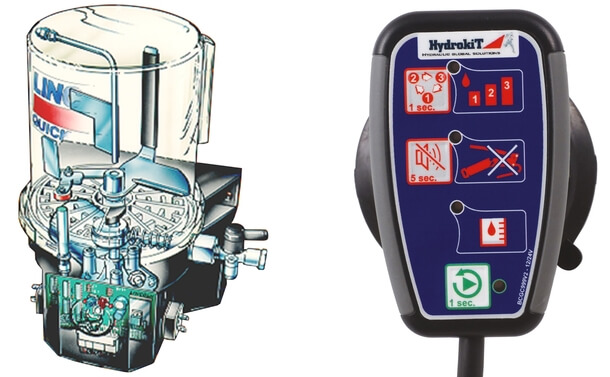
Automatic lubrication with hydraulic source
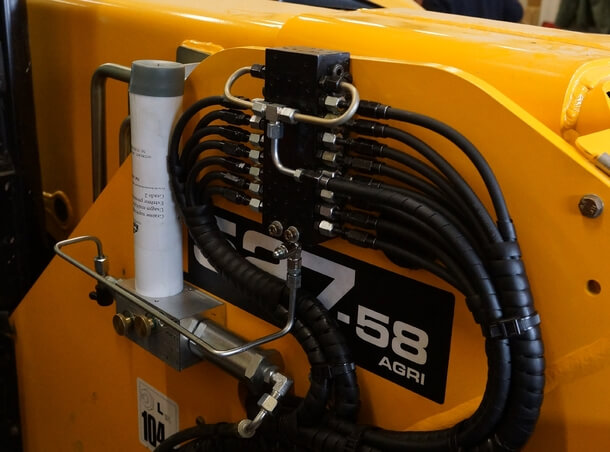
The pluses:
-
Economical: cheaper pump, standard cartridge
-
Easy to install and versatile: no electrics
-
Optimised lubrication: lubrication only works when the machine's hydraulic function is activated
-
More compact
Circuit version with free return
-
The pump is activated by the machine's hydraulics: the lubrication is active and continuous as long as the hydraulic function is active
-
Better compliance with the lubrication plan
-
Applications for mini-excavator, carriage, telescopic handler, unloader
Single-acting circuit version
-
The pump is activated by the machine's hydraulics: A dose of grease is sent each time the hydraulic function lever is activated (one dose of grease per pressure rise)
-
Versatile
-
Applications for trailers (lubrication during tipping), ploughs, ...
Graissage pour marteau piqueur
The pluses:
-
Longer hammer life
-
Better hammer operation (continuous lubrication)
-
Autonomous: the pump remains on the tool to be lubricated, even when the carrier device is replaced
-
Practical: changing the cartridge is very quick and simple - Compact: easy to position on small hammers (model PGPMART02L)
Operation: The lubrication pump is attached to the hammer: lubrication takes place while the hammer is running, driven by the hydraulic system of the device.
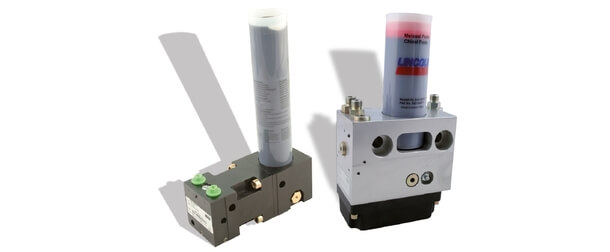
Greasing of telescopic carriage
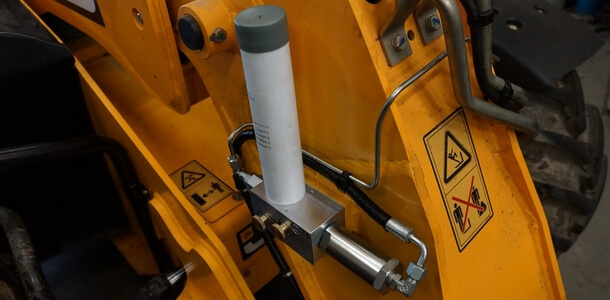
The pluses:
- Reduction of maintenance costs: when there is a lack of lubrication, parts tend to seize and need to be changed (axes, etc.)
- Time saving: lubrication is carried out automatically during the operation of the machine (automatic version) or is to be carried out regularly at a single point by grease gun (single-point version)
- Longer life of the equipment
- Optimised greasing at strategic points of your telescopic handler
Automatic single-point gas lubrication
The pluses:
-
Integrated gas operation: no power supply required
-
Suitable for the toughest conditions: ATEX certified for zone 0
-
Continuous and long-lasting lubrication: works even when the machine is at a standstill, dispensing time up to 12 months
Operation
-
The lubricator consists of a transparent reservoir filled with a specified lubricant and a cartridge containing an electrochemical gas cell. Once activated, the internal batteries are electrically connected and gas production can begin. The piston moves as the pressure increases pushing the lubricant into the application.
-
The rate of gas production is proportional to the electric current
-
Each position of the dial is designed to allow a given flow of current, thus setting the distribution time from 1 to 12 months
Features
-
Max. pressure 5 bar
-
7 greases formulated for temperatures from -45 to +150 °C
-
5 chain oils
-
ATEX zone 0 certification (inert gas)
-
Distribution period from 1 to 12 months
-
Lubricant visible during use
-
Capacity: 60 and 125 ml
-
IP 68 protection
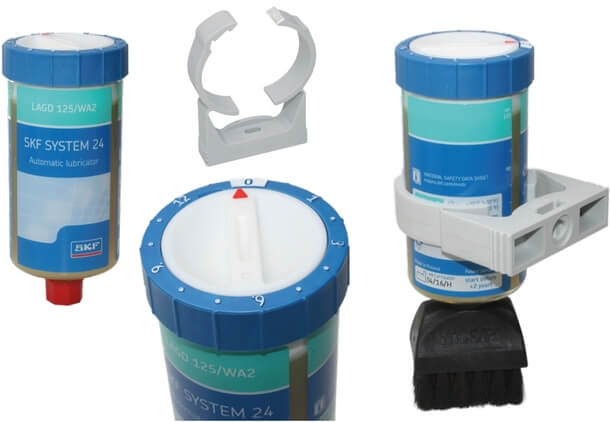
Automatic single-point lubricator
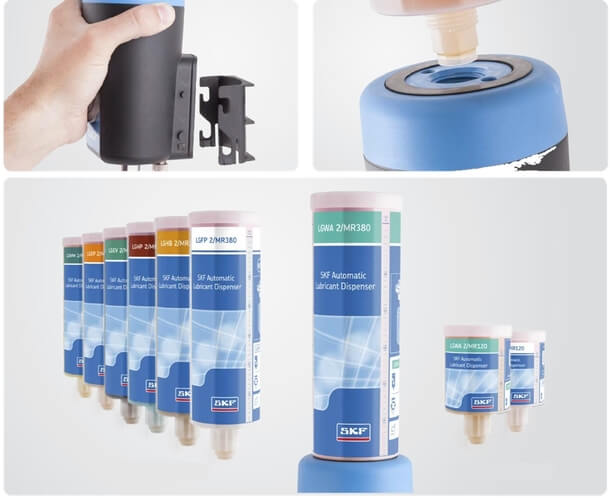
The pluses:
-
Practical: autonomous over a long period
-
Simple: screw-in cartridges
-
Versatile: adjustable flow rate from 0.16 ml/day to 12.5 ml/day, i.e. from 1 to 24 months
-
Safety: monitoring screen (ON/OFF - pause - low level - lock)
Operation
-
An electric motor drives a piston feeding 1 outlet. The operating cycle can be adjusted for lubrication for up to 24 months without changing the cartridge, for automatic lubrication of isolated or dangerous access points.
-
Compact design, robust for applications with large temperature variations (-25°C to +70°C) or vibrations, dust and waterproof (IP67).
Technical specifications
-
Max. pressure 30 bar
-
9 greases formulated for temperatures from -25 to +70 °C
-
Up to 5 metres of offset
-
Distribution period from 1 to 24 months
-
Lubricant visible during use
-
Capacity: 120 and 380 ml
-
IP 67 protection
-
Powered by 4 AA or external 12/24V batteries